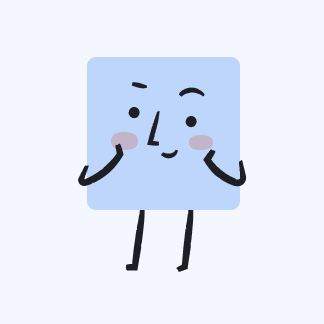
Creating a process flow diagram for stock management involves outlining the steps that inventory goes through from the initial purchase order to the final sale. Below is a detailed explanation of each step in the process: Please summarise below. ### 1. **Purchase Order (PO)** - **Description**: A purchase order is created when a business decides to buy stock from a supplier. This document outlines the items, quantities, prices, and delivery terms. - **Details**: - The purchasing department identifies the need for stock based on inventory levels or sales forecasts. - A PO is generated and sent to the supplier for approval. - The supplier confirms the order, and the PO is recorded in the system. ### 2. **Bill from Supplier** - **Description**: Once the supplier ships the goods, they send a bill or invoice for the items delivered. - **Details**: - The bill includes details such as item descriptions, quantities, prices, and payment terms. - The accounts payable department verifies the bill against the PO and the received goods to ensure accuracy. ### 3. **Stock Rises** - **Description**: Upon receiving the goods, the stock levels in the inventory system are updated to reflect the new quantities. - **Details**: - The receiving department checks the items against the PO and the bill. - Any discrepancies (damaged goods, incorrect quantities) are reported and resolved. - The inventory management system is updated to increase stock levels accordingly. ### 4. **Sales Order (SO)** - **Description**: A sales order is created when a customer places an order for products. - **Details**: - The sales team enters the customer’s order into the system, specifying the items, quantities, and delivery details. - The sales order is confirmed with the customer, and the order is queued for fulfillment. ### 5. **Invoice Generation** - **Description**: An invoice is generated based on the sales order once the products are ready for shipment. - **Details**: - The invoice includes details such as item descriptions, quantities, prices, taxes, and payment terms. - The invoice is sent to the customer, and it serves as a request for payment. ### 6. **Inventory Drop** - **Description**: When the products are shipped to the customer, the inventory levels are decreased to reflect the sale. - **Details**: - The fulfillment team picks and packs the items for shipment. - The inventory management system is updated to decrease stock levels based on the sales order. - This step ensures that the available stock reflects the actual inventory on hand. ### 7. **Stock Reorder** - **Description**: If stock levels fall below a predetermined threshold, a reorder process is initiated to replenish inventory. - **Details**: - The inventory management system monitors stock levels and triggers alerts for low inventory. - A new purchase order is created to restock items, following the same process as the initial purchase order. ### 8. **Production (if applicable)** - **Description**: If the business produces its own goods, this step involves manufacturing products to replenish stock. - **Details**: - Production planning is based on sales forecasts and current inventory levels. - Raw materials are procured, and the production process is initiated. - Once production is complete, the finished goods are added to inventory, increasing stock levels. ### 9. **Sold** - **Description**: The final step in the process is the completion of the sale, where the customer pays for the goods. - **Details**: - Payment is received from the customer, either upfront or on credit. - The sale is recorded in the accounting system, and the transaction is marked as complete. - Customer records are updated, and any follow-up actions (like delivery confirmation) are initiated.
Solución ThothAI de Upstudy
Respuesta rápida
Solución paso a paso
Introduce tu pregunta aquí…